Вчені виростили найбільший у світі кристал
Коломия ВЕБ Портал | Публіцистика та аналіз | 2009-08-13 11:41:32
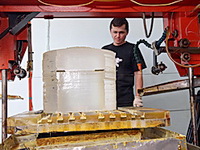
Півтонни чистої ваги у випадку зі штучним кристалом — рекорд, без сумніву, знаковий. Але фахівці Інституту сцинтиляційних матеріалів, що входить до складу НТК "Інститут монокристалів", здивували світ не тільки масою свого масштабного дітища, а й його унікальними властивостями. Завдяки харківському ноу-хау техніка для митного огляду, встановлена в аеропортах та на митницях, стала більш "пильною", дешевою і зручною у використанні.
Усе своє — технологія, виробництво, якість. Кількість країн, що спроможні самостійно вирощувати штучні кристали, можна перерахувати на пальцях однієї руки. Цей процес надто копіткий, витратний і наукоємний. Україні унікальне "господарство" дісталося у спадок від колишнього Радянського Союзу. Тому молоді науковці, які днями презентували свою новинку, не схильні "тягнути ковдру на себе". Кажуть, до створення гігантського красеня причетні одразу три покоління харківських учених. А їм вдалося півстолітню працю попередників реалізувати за допомогою нової технології, яку розробили самі.
Найбільший її плюс — актуальність на міжнародному ринку. Елементи подібних кристалів у рентгенівській доглядовій техніці використовують уже давно. Власне, саме завдяки їм такі прилади і можуть виявляти заборонені для транспортування вантажі в аеропортах, на митницях, поштових відділеннях. Але річ у тім, що вмонтовані в уже діючі детектори кристалічні фрагменти досить дорогі. До того ж через складність процесу їх виготовлення на міжнародному ринку виник певний дефіцит ком¬плектуючих для доглядової техніки. А ті, що є, не відповідають усім запитам споживачів.
Найбільша Ахіллесова п’ята цих виробів — низький рівень післясвітіння. Тобто кристали від інших виробників не можуть швидко (за десяті частки секунди) "забути" про випромінювання, які вони зафіксували раніше, тому наступна картинка на моніторі може бути змитою. Щоб не проґавити заборонений для транспортування предмет, доглядовим службам доводиться розтягувати процедуру перевірки у часі, випробовуючи терпіння пасажирів. Унікальність харківського велетня якраз і полягає в тому, що він вразив не лише пристойним розміром та вагою (хоча це теж серйозна виробнича перевага), а й спроможність радикально вирішити згадані вище проблеми.
"Наш метод виробництва — найшвидший у світі, — розповідає завідувач сектору вирощування монокристалів Володимир Таранюк. — До того ж розроблена нами технологія дозволяє контролювати у процесі росту кристалу різноманітні параметри цього продукту, задаючи йому потрібну властивість. А головне — кристал має дуже низький рівень післясвітіння. Тобто за долі секунди "забуває", що з ним відбувалося раніше і готовий виконувати роботу знову. Ця його властивість справді унікальна і не має аналогів у світі".
Вага харківського велетня — 504 кілограми. Росте він 18–19 діб на основі звичайнісінької кримської солі, після чого його ріжуть на дрібніші частини. Розмір останніх залежить від функціонального призначення детекторів, для яких виготовлять кристалічні комплектуючі. Це може бути і "дріб’язок", тотожний розміру сірника, і солідна деталь, вагою 25 кілограмів.
Процес вирощення продукту, його порізка на потрібні фрагменти і багатоступінчастий контроль за якістю — єдина технологічна лінія, яку, знову ж таки, розробила команда молодих науковців інституту. "Ми поставили перед собою завдання об’єднати всі процеси технології вирощування кристалів у єдиний виробничий комплекс для того, щоб він функціонував максимально ефективно, — каже завідуючий відділом контролю якості Єгор Андросов. — В основі всього — орієнтація на міжнародні стандарти і західного споживача".
В Україні, на жаль, харківські кристали не користуються попитом. І це при тому, що держава потребує оновлення доглядової техніки і має чимало підприємств, здатних її виробляти.
Картинка у реальному часі. Детектори з кристалічною начинкою можна використовувати в усіх приладах, що працюють на основі радіоактивного випромінювання. З його допомогою кристал "бачить" живу картинку досяжної йому реальності і передає її на екран. Звідси фактично безмежна сфера використання цього продукту — атомна енергетика, геологія, комунальна галузь, медицина. Скажімо, виготовлені на основі кристалічних детекторів гама-камери здатні замінити теперішній рентген, оскільки діагностують без знайомої плівки, в режимі "он-лайн". Таку техніку вже широко використовують на Заході, а до нас вона лише починає пробивати свій шлях. Як, до речі, і прилади для пошуку та діагностики ракових захворювань, створені у тому числі й на основі харківських кристалів. В Україні їх теж сьогодні — одиниці.
Вийти на міжнародний ринок Інституту сцинтиляційних матеріалів допоміг скрупульозний підхід до якості, яку молоді науковці по-сучасному "вознесли" до рівня окремого елемента своєї розробки. "Коли ми купуємо складну побутову техніку, нам видають на неї гарантію, — каже Єгор Андросов. — У даному випадку це означає безкоштовну заміну неякісної деталі. Таке розуміння гарантії неприпустиме для рентгенівських доглядових сканерів. Важко навіть уявити, що відбудеться, коли на митному пункті чи на терміналі великого аеропорту вийде з ладу така техніка хоча б раз на добу! Тому для настільки "відповідальної" апаратури потрібен зовсім інший рівень якості виробів. Знайдене нами технічне рішення дозволяє вирішити проблему контролю до одного мільйона детекторів на рік, і гарантує, що в кожній тисячі поставлених детекторів виявиться не більше одного (!), який не відповідає технічним вимогам. Це справді вагомий результат".
І ще одне ноу-хау. Створюючи свою технологічну лінію, молоді науковці зрозуміли, що існуючий спосіб механічної обробки великих детекторів абсолютно не придатний для виготовлення елементів малого розміру, оскільки погіршує поверхневі характеристики певних шарів кристалу. Аби вирішити цю проблему, харків’яни розробили власну технологію обробки, яка не потребує доведення виробу до потрібної кондиції вручну. Усе робить спеціальна техніка без участі людини.
Свою технологію харків’яни створили і застосували на практиці за рекордні три роки. З такою ж швидкістю вона завоювала популярність фактично в усіх куточках світу. Продукцію інституту сьогодні купують американські, європейські і навіть японські фірми, де виробництво монокристалів вважається пріоритетним напрямом розвитку науки.
Новий рекорд! Але не єдиний. Соляний гігант Інституту сцинтиляційних матеріалів — не єдиний харківський монокристал, який побив світовий рекорд своїм розміром. Наприкінці минулого року у стінах цього ж науково-технічного комплексу був вирощений найбільший на планеті кристал сапфіра. Його вага 50 кілограмів, довжина — 80 сантиметрів.
У живій природі цей коштовний камінь трапляється нечасто. Але оскільки він за міцністю поступається лише алмазу, потреби в сапфірах досить великі. Саме тому технології вирощення штучних сапфірових кристалів почали розробляти ще на початку минулого століття. І ось недавно харків’янам вдалося створити ще й по-справжньому об’ємний продукт. Запропонована вченими технологія дозволяє вирощувати найбільші і найдешевші сапфіри високої якості. Вони, без перебільшення, не горять у вогні, і у воді не тонуть. Тобто не плавляться навіть у мартені, не розчиняються у кислоті, не руйнуються в епіцентрі ядерного вибуху. Хоча практичне їх застосування досить мирне. Вже невдовзі на основі елементів штучного сапфіра будуть створені електричні лампочки нового покоління, які споживають порівняно невелику кількість струму і горять не лічені місяці, а роки.
Справжню революцію сапфірові кристали принесли і в медицину, витіснивши металічні імплантанти. Їх використовують скрізь, де потрібні замінники кісткової тканини, — у стоматології, ортопедії, пластиці хребта. Це стало можливим завдяки тому, що сапфір гармонійно приживається всередині організму, бо він не токсичний, не викликає зміни функцій внутрішніх органів, не змінює характеристики білкового та жирового обміну. Тобто біоінертний і біосумісний. Сьогодні в інституті вже налагоджено дільницю з виробництва найрізноманітніших імплантатів, які повернули здоров’я тисячам пацієнтам як вітчизняних, так і зарубіжних клінік.
Автор: Лариса САЛІМОНОВИЧ, "Україна молода"
Обговорити на форумі